Manage manufacturing with an easy-to-use MRP software
QT9™ ERP makes it easy to manage material requirements, from production planning and scheduling to purchasing and inventory control.
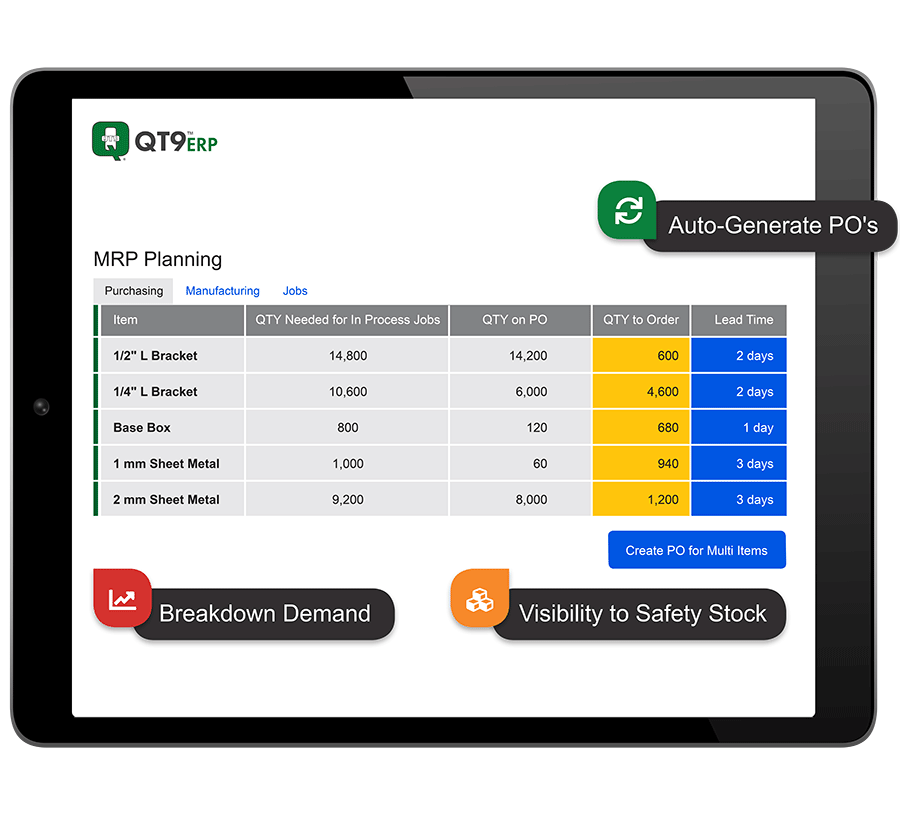
Connect material requirements to the rest of your business
Empower employees, departments and locations to work as one.
Increase scalability
Automate manual tasks by eliminating outdated paper spreadsheets and paper logs.
Just-in-time
Reduce costs
Simplify material planning
Continuously maintain adequate levels of inventory and prevent shortages by adjusting to changing demand requirements with the QT9 ERP.
-
Streamline inventory management by synchronizing available inventory, inventory in transit, reorder quantities and inventory costs using advanced material requirement planning features.
-
Put inventory control on autopilot by auto-allocating inventory and automating inventory level notifications to prevent shortages.
-
Scale inventory levels to match demand using real-time results for better planning and production scheduling by MRP software.
-
Easily see purchasing and manufacturing requirements at the click of a button.
-
Enable multi-location inventory tracking to track inventory across locations.
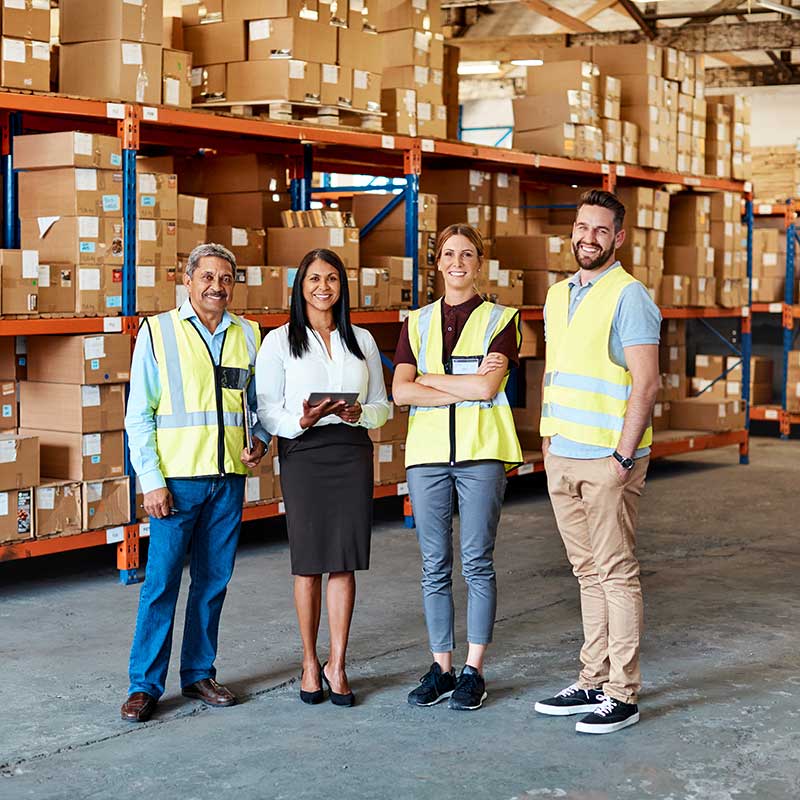
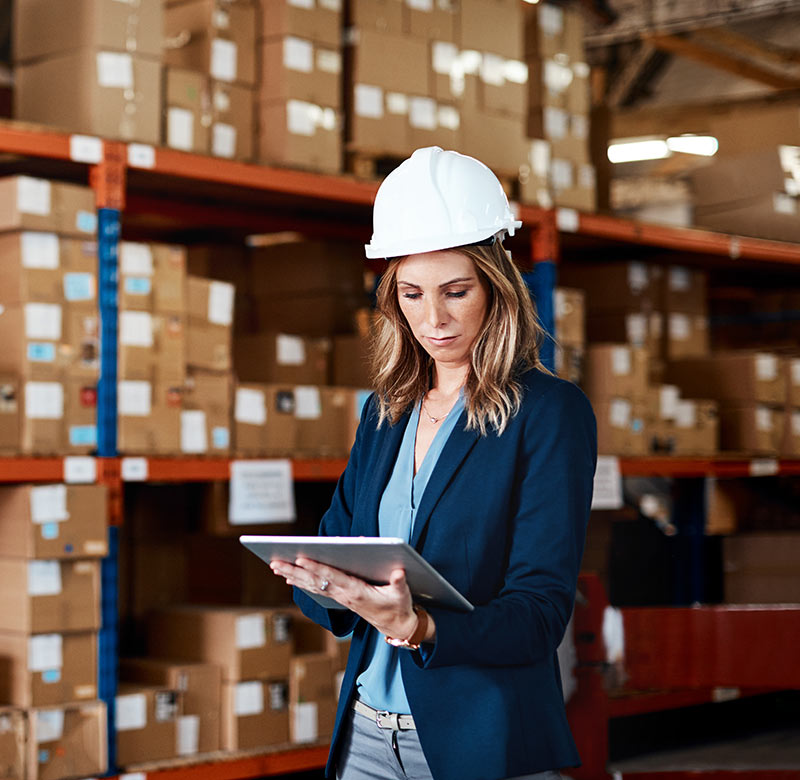
Modernize planning
Seamlessly manage all aspects of planning from one central place and accelerate productivity with the integration of new technology.
-
Auto-create purchase orders with the click of a button in the MRP planning module which supports material requirements planning.
-
View production requirements, sales order requirements, inventory levels, current purchasing levels and even lead times in one screen.
-
Use the Supply & Demand Tool to forecast material needs based on open jobs and demand.
-
Plan by date, by job or even by total system demand.
-
Export MRP planning to Excel for further analysis.
-
Ensure accurate planning with integration to active Bill of Materials.
Streamline purchasing
QT9 offers a holistic MRP software specifically created for manufacturing that lets you know exactly what to buy and when to buy it. Purchase only what you need.
-
Optimize supply chain management by synchronizing purchase orders, receipts, invoices and returns.
-
Minimize manual data entry by automatically populating purchase orders with supplier part numbers, descriptions and even tiered pricing.
-
Reduce costs by planning purchases based on vendor discounts, shipping, surcharges and taxes.
-
Plan purchases in real-time with dynamic dashboard grids that show your purchasing activity from unprocessed POs to open PO items.
-
Simplify the receiving queue by splitting your POs in case of a back order, receive short or extra material and attach files to purchase order items (including C of As).
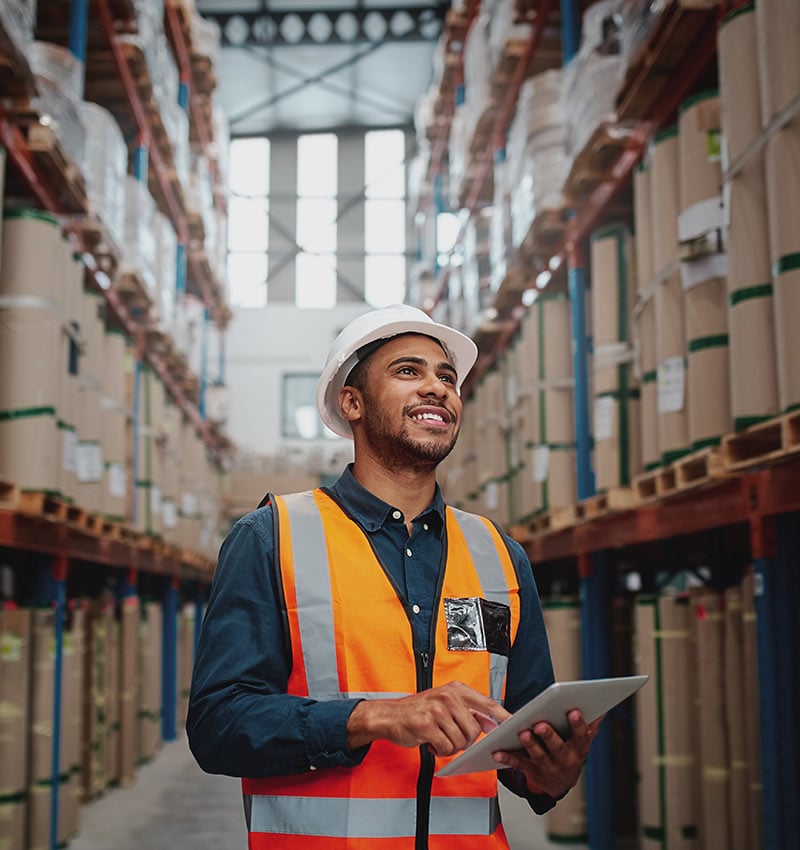
Manage all your MRP needs from one solution
Everything you need from MRP software.
FAQs
What is Material Requirements Planning (MRP)?
MRP is the process of determining the appropriate types and amounts of materials needed to produce a good and ensuring those materials are available when they are needed for production. The process consists of three primary steps: inventorying materials on hand, identifying what additional materials are needed, and then scheduling their production or purchase so that they arrive on time and in the right place so operations can proceed smoothly.
What is MRP software?
MRP software calculates the materials needed to meet production plans and customer demand using data from lead times, sales forecasts and production plans to determine the optimal stock levels. With MRP software, companies can easily view production requirements, stock on hand and purchasing or production needs, as well as historical purchasing and production data.
Who needs MRP software?
An MRP system can be used in different manners depending on the type of business, its products and its fulfillment approach – make to order or make to stock. For manufacturing, MRP software almost always utilizes a Bill of Materials (BOM) to determine the parts and components a business will need to purchase or manufacture to create a product. A BOM is the ultimate record of the these items. It gives manufacturers and inventory control experts a plan by which to begin gathering materials.
What is the difference between MRP and ERP?
MRP is often a function of an ERP system, working in conjunction with many standard ERP functions, including purchasing, production scheduling, inventory control, BOM management and compliance.
How does QT9 ERP support Material Requirements Planning (MRP)?
QT9 ERP is a comprehensive MRP software that simplifies material requirements planning by centralizing it with pertinent manufacturing and enterprise-wide functions.
Overall, QT9 ERP improves efficiency and accuracy by centralizing and integrating data and automating operations.
With QT9 ERP you get:
- 17+ modules, including Inventory Control and Supplier Management
- Customer, compliance, supplier and physical inventory web portals
- Lot and serial number inventory control
- Tailored customer support
- Real-time reporting with mobile accessibility
- Seamless integration with QT9 QMS quality and compliance software
Reach out today for a demonstration or to get started with a free trial.
Experience QT9 ERP in action today
Schedule your personalized demo and start a free trial.